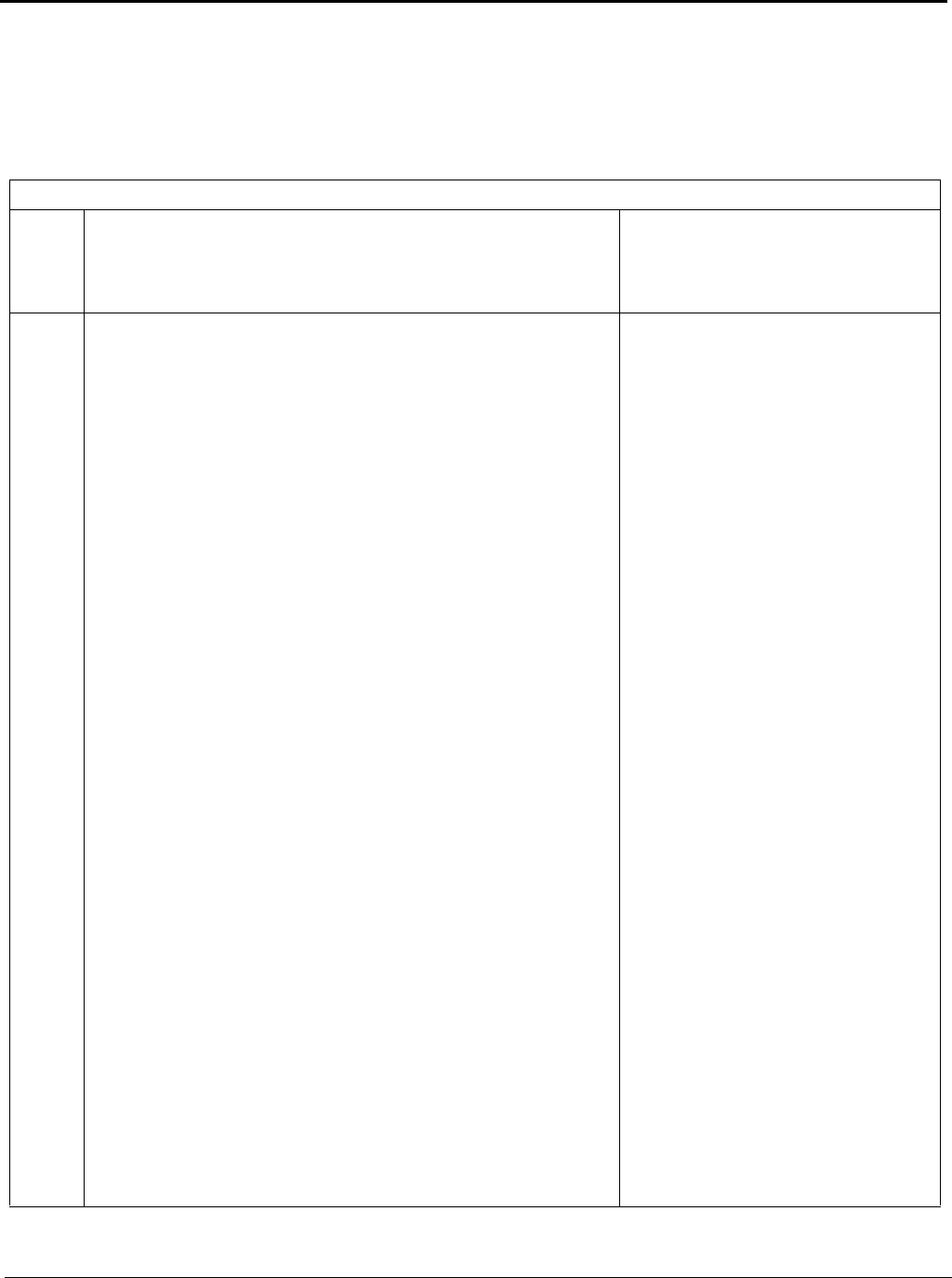
Appendix H: U.S. Bauxite and Alumina Quantities, 1960-2003
Table H.1: U.S. Supply of Bauxite and Alumina from 1960 to 2003 (in Thousand Metric Dry Tons)
A B C D E F G H I
Year
Imports
of Bauxite
U.S.
Mined
Bauxite
Exports of
Bauxite
Net
Bauxite
Supply
Estimated
Alumina
Production
from
Bauxite
Imports
of
Alumina
Exports
of
Alumina
Estimated
Net
Alumina
for
Electrolysis
1960 8,879 2,030 29 10,880 4,651 80 4,266
1961 9,354 1,248 153 10,449 4,467 171 4,191
1962 10,745 1,391 263 11,873 5,076 158 4,726
1963 9,408 1,549 206 10,751 4,596 173 4,309
1964 10,518 1,627 283 11,862 5,071 191 4,755
1965 11,601 1,681 149 13,133 5,614 206 290 4,969
1966 11,928 1,825 63 13,690 5,852 443 290 5,420
1967 12,010 1,681 2 13,689 5,852 865 499 5,633
1968 11,359 1,692 7 13,044 5,576 1,190 780 5,429
1969 12,355 1,873 5 14,223 6,080 1,730 885 6,317
1970 13,039 2,115 3 15,151 6,477 2,340 998 7,171
1971 12,837 2,020 35 14,822 6,336 2,190 980 6,913
1972 12,803 1,841 29 14,615 6,248 2,590 797 7,416
1973 13,618 1,909 12 15,515 6,633 3,090 694 8,365
1974 15,216 1,980 16 17,180 7,344 3,290 927 8,973
1975 11,714 1,801 20 13,495 5,769 3,180 933 7,439
1976 12,749 1,989 15 14,723 6,294 3,290 1,050 7,905
1977 12,989 2,013 26 14,976 6,402 3,760 857 8,665
1978 13,847 1,669 13 15,503 6,628 3,970 878 9,057
1979 13,780 1,821 15 15,586 6,663 3,840 849 8,988
1980 14,087 1,559 21 15,625 6,680 4,360 1,140 9,232
1981 12,802 1,510 20 14,292 6,110 3,980 730 8,749
1982 10,122 732 49 10,805 4,619 3,180 590 6,747
1983 7,601 679 74 8,206 3,508 4,030 602 6,585
1984 9,435 856 82 10,209 4,364 4,290 648 7,570
1985 7,158 674 56 7,776 3,324 3,830 316 6,506
1986 6,456 510 69 6,897 2,948 3,600 487 5,767
1987 9,156 576 201 9,531 4,075 4,070 1,130 6,607
1988 9,944 588 63 10,469 4,475 4,630 1,040 7,618
1989 10,893 W 44 10,849 4,638 4,310 1,330 7,154
119