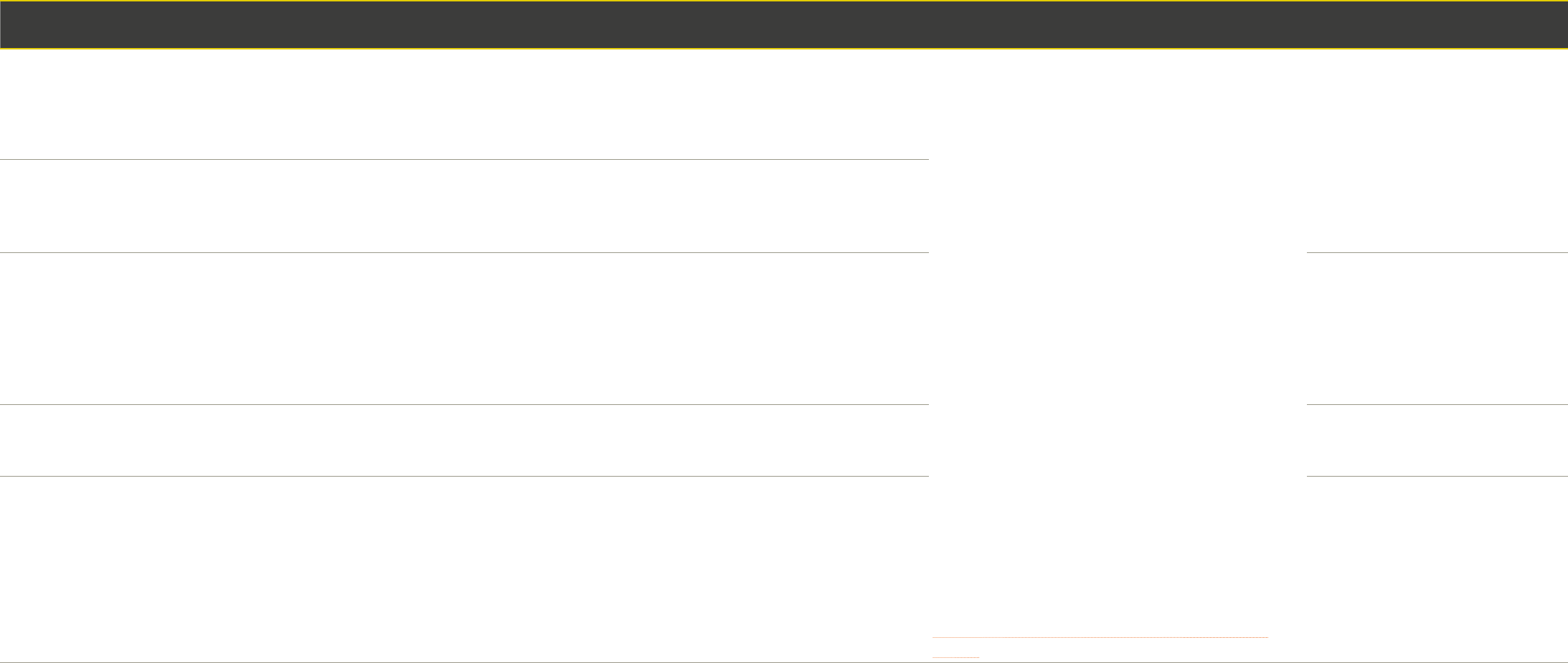
STAKEHOLDER CONSULTATION PAPER 33
Table 3: Comparison of State Insulation Schemes – Sample of Pre and Post Insulation Installation Safety Requirements
19
PROGRAM OUTLINE AMBITION, TIMING PRE-INSTALLATION ELECTRICAL
SAFETY CHECK
SAFETY COMPETENCY REQUIREMENTS – INSULATION
INSTALLERS
POST INSTALLATION AUDITING
Stay Warm SC (SWSC) Program,
NSW
The SWSC program provides
insulation upgrades to
households in the Riverina
region.
Reached ~700 households between April
2010 and August 2013.
Pre-installation electrical safety
inspection, by a licensed electrician.
Insulation installers have to have received training in how to
identify and manage electrical safety risks. They have a duty
to still check, identify and report any electrical risks in line
with the installation Australian Standard (AS3999:2015).
All programs require insulation installers to have Clean Energy
Council Insulation Installer Accreditation.
Clean Energy Council Accredited Insulation Installer Training
requirements.
Installers must have received training on the full content of
the bulk thermal insulation–installation Australian Standard
(AS3999:2015). On completion of this training, installers
must demonstrate their achieved competency by passing a
comprehensive written and practical assessment.
The course covers five units of competency from the
Certificate III in Wall and Ceiling Lining (CPC31211):
→ CPCCOHS2001A Apply OHS requirements, policies and
procedures in the construction industry
→ CPCCCM1015A Carry out measurements and calculations
→ CPCCCM2010B Work safely at heights
→ CPCCPB3014A Install batt insulation products
→ CPCCPB3027A Install ceiling insulation.
To receive standard ceiling accreditation, installers will have
to complete the industry training (units from the Certificate
III in Wall and Ceiling Lining as listed in Section 7.1), provide
evidence of three completed ceiling insulation jobs and pay
an annual subscription fee. For further information on the
CEC insulation accreditation program and accreditation
process.
The first 3-5 jobs are audited for new
installers immediately by insulation
auditors (not electricians) to ensure
they are following protocols. Then the
program moves to, “10% of insulation
jobs have an onsite audit/ inspection
and report conducted by an NSW
Government approved contractor/s
who is independent of the insulation
contractor/s.”
Home Energy Action –
Community Housing, NSW
The HEA program is designed
to deliver energy eiciency
improvements to households in
need, across NSW.
Upgraded ~2500 community housing
properties (dwellings) in 2016–17.
Pre-installation electrical safety
inspection, by a licensed electrician.
Latrobe Valley – Energy Upgrade
Program
Targeting low income
households/households with
disability.
Provides energy assessment.
If insuicient insulation,
insulation is provided as part of
the upgrades.
100 insulation upgrades in total Pre-installation safety check by insulation
installers with Clean Energy Council
Insulation Installer Accreditation to
comply with the Australian Standard
(AS3999:2015) for bulk insulation
installations.
DELWP / Sustainability Victoria
Partnership to deliver.
Audit of the first 3-5 installs of each
installer. 20-25% of the 100 to be audited.
No licensed electrician
Aordable retrofits program,
DELWP
100 homes Licensed electrician does the pre-
installation inspection.
100% audited
Specialist insulation auditor
Healthy Homes, Victoria –
Sustainability Victoria
Energy assessment to identify
need. Insulation upgrade is
delivered by an independent
company hired by Sustainability
Victoria.
1000 to be delivered in 2018-2019
Mid 2018 start
Clean Energy Council accredited
Insulation Installers undertake the
electrical safety check to comply with the
Australian Standard (AS3999:2015) for
bulk insulation installations.
Insulation auditors.
10-20% of all upgrades.
This equates to the first 2 jobs by each
installer – and possibly one addition one.
19 Note: All Schemes do not use foil insulation, all retain direct control - over procurement processes and standards through programs.