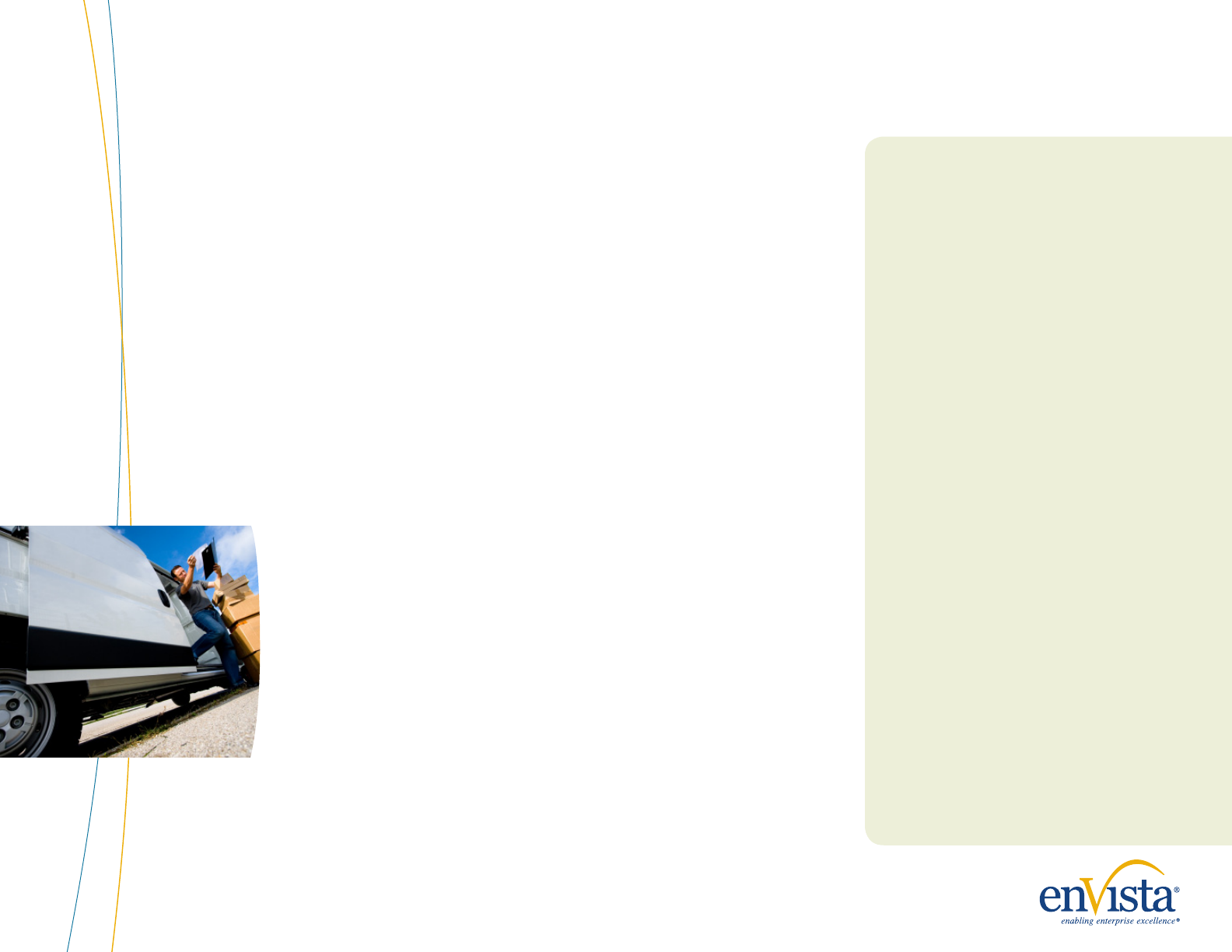
Slot Type
Slot type denes the type and dimensions of
a storage medium. Typical slot types include
shelving, decked rack, case ow, pallet rack,
and pallet ow of varying dimensions. Slot
type is critical to slotting for space, equipment,
replenishment and picking considerations.
In a primary pick model, the number of
replenishments is a function of item cube,
throughput, and storage cube size. An
undersized pick face will cause excessive
replenishment, resulting in higher operating
costs. An oversized pick face is a waste of
space and the resulting operating cost of the
space. An oversized pick face, in
most cases, will also introduce
picking ineciencies in the form
of additional travel time. A balance
should be sought between
replenishment and picking labor
cost, space available and cost.
Additionally, slot type is a factor in
the pick rate. The overall cumulative
slot type prole is more or less
relative toward a higher density
or lower density pick zone. A high-density
pick zone is more ecient for picking, but will
hold less product. A low density pick zone will
require greater travel distance, and therefore,
is less ecient for picking, but will hold more
product. This is the third variable to factor into
the equation.
To determine slot type, use the output from
the material ow analysis and warehouse
conguration information, both current and
proposed, to determine a slot type by item.
This then becomes the primary slotting criteria.
ABC Velocity Rating
The ABC velocity rating is output from the
material ow analysis. The output represents an
ABC rating for each SKU with “A” representing
fast movers and “C” representing slow movers
in terms of “hits” or “lines per day.”
Velocity slotting primarily reduces travel time.
The objective is to minimize the pick path or
travel distance required to pick an order, a
cluster of orders, or a batch. This is done by
grouping product by ABC rating, with an “A”
representing the fastest moving items in the
warehouse, and “C” the slowest. Additional
ratings are usually added for very slow “D”
items. ABC slotting is combined with slot type
and order commonality (discussed below) to
balance labor and space costs and produce the
optimal slot plan.
Additional Criteria
• Order commonality is a group of items likely
to ship together on the same order. This
group is then slotted together or close by
within a specic slotting zone.
• Base product applies to picking-to-pallet.
In a pick-to-pallet using an order picker,
pallet jack or lift truck, the challenge is to
build the pallet while picking and avoid
the double handling of pallet rebuild and/
or consolidation at the shipping dock. In
this slotting criteria, the base product that
is the heaviest and/or bulkiest is placed rst
within the pick path. The slotting may have
intermediate zones, but, in any case, the
lighter and/or smaller product ends up on
the top of the pallet. If base is a criterion, it is
usually the primary slotting criterion and all
others, including velocity, are subordinate.
• Source slotting or slotting by vendor is
sometimes used to help minimize putaway
labor by grouping items together from the
same vendor. This applies more to mixed-
pallet receiving.
• Customer slotting refers to grouping items
together that are more or less customer
v i e w p o i n t
Successful Warehouse Slotting